Have you ever had any concerns at a production site?
- The quality differs depending on the workers
- Visual inspections inevitably result in omissions
- Lacking personal skills in digital area
- Want to check the quality of work during the assembly process
- Want to ensure traceability in case defects occur
RICOH serves you the smart camera that is capable of preventing work errors by automatically checking the status of manufacturing operations to assemble parts and other components through the use of image recognition technology.
Choose RICOH SC-20 is the easy way to start the digital inspection process
- Digital image inspection during or after a job
(High precision shape, color, and texture judgements with high resolution images) Image recognition automatically assembly status during the work. Digitalization of visual inspection helps maintain consistency and prevent mistakes - Batch Inspection after a job completed
To make sure instructions were followed correctly. Inspection can also be conducted before proceeding to the next step. If any part of the job doesn’t match the instruction steps or if a part is missing etc., fail appears along with the applicable location, this prevents the worker from proceeding to the next step until the mistake has been corrected
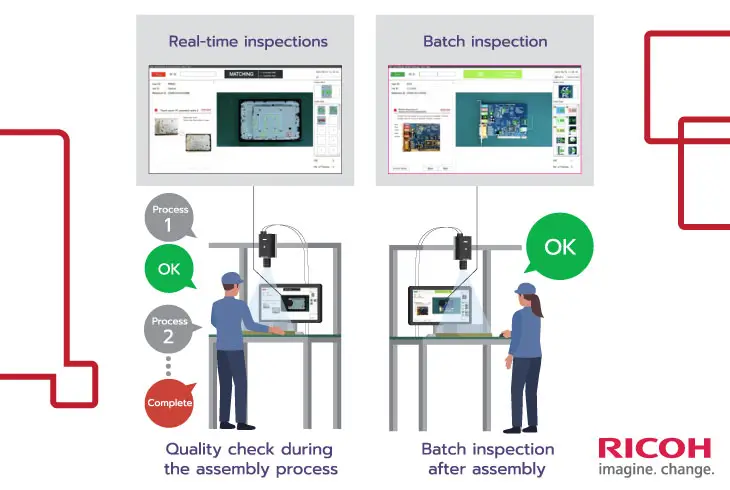
- Easy installation without the need for computer
The system is easy to set up if you have a mouse, keyboard and monitor, integrate camera, image processing engine and software. It can be connected to various external devices such as the external connector, Lan port, Bluetooth etc. - Ensure traceability
Part serial numbers, work times and inspection results can be recorded to an SD card or shared network folder, for use in work analysis and traceability
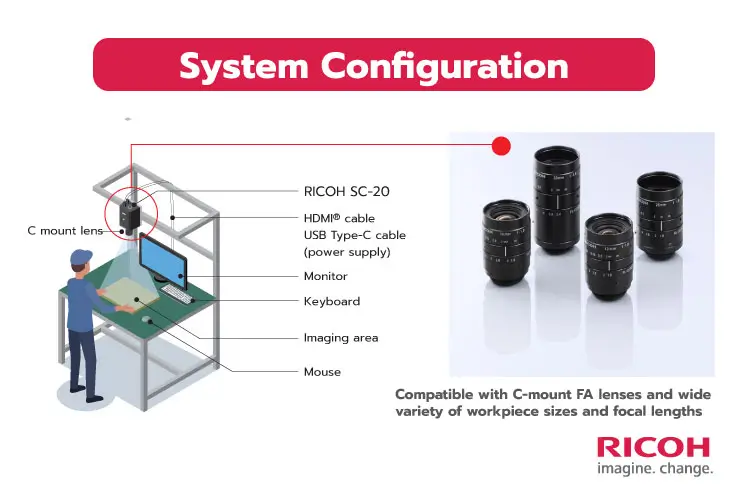
The camera uses an interchangeable C mount lens, select from resolution, minimal distortion RICOH machine vision lens focal lengths to match the size of your work piece
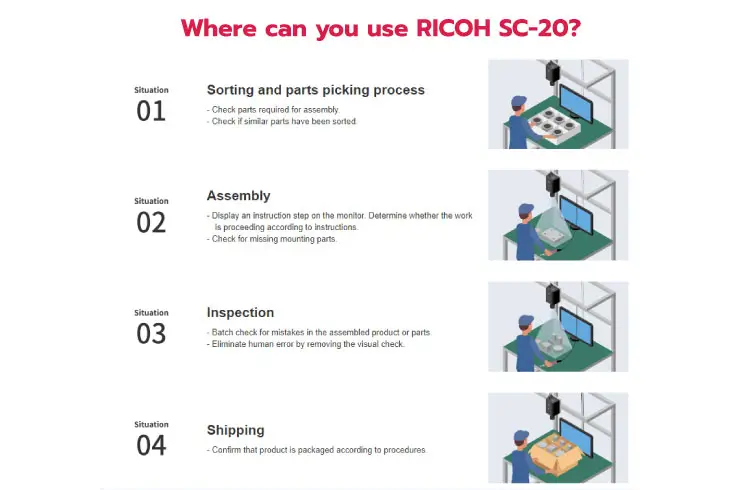
Example cases
Issue 1: Reducing man-hours
Before: Sorting work and visual inspections lead to more steps, man-hours were required to sort parts in advance at this particular factory
After: Digitalizing missing part measures eliminates sorting work, improving production and eliminates about 40 minutes of man-hours

Issue 2: Improving defect rates and reducing man-hours
Before: Average visual inspection man-hours of 2.57 seconds per board
After: Average of 0.88 seconds result in a 65.8% man-hour reduction
High precision image recognition, resulting in a zero-defect rate, eliminating waste parts
Let’s connect
Get in touch with one of our consultants and find out how we can help you create your hybrid workplace.